Keeping a construction project within budget is nearly always a challenge; but trying to do so in a largely unpredictable economy presents a whole new set of challenges. When your district is conducting pre-referendum planning but not starting construction for two to three years, how do you build possible financial scenarios into the budget? Here are four factors that can lead you on a path to success, highlighted with examples from Clintonville Public School District (CPSD) in Wisconsin.
CPSD completed planning and pre-referendum work in 2020, conducted project bidding in 2021, and built the following two years. During this time, they experienced supply chain challenges, staffing trials, and increasing inflation. These issues could have brought the project to a standstill, but you’ll see the steps we took together that ultimately made the project a success.
PRIORITIES
Be certain, from the start, that you have a prioritized statement of goals. Some facets of a project may be non-negotiable, so make your team conscious of what those are. Keep in mind that if everything is a priority, nothing is a priority. Be practical and open about what matters most.
Different projects have different prominence or aim. Some district’s activities are focused on improving specific curriculum, while others may highlight increasing student safety. For some, their main goal may be to enhance or maintain the infrastructure of the buildings. Having conversations with stakeholders during the planning stage provides a much needed “guiding light” for your design and construction team.
In the case of Clintonville Public School District, the priority of the project was to prepare students for the workforce and to provide safe facilities that were conducive to today’s instruction.
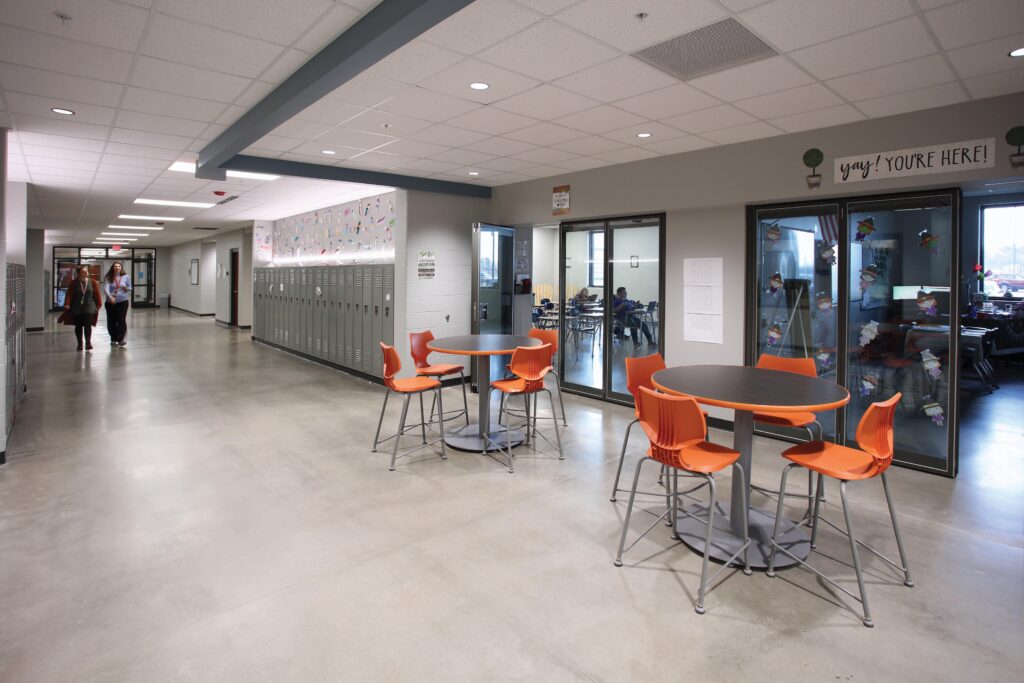
CONSTRUCTION TIMING & SEQUENCING
Breaking your project into manageable portions will provide you with the needed options to pivot or modify scope if needed to stay on budget or schedule. Looking at your school’s masterplan comprehensively will allow you to envision how you might shift if needed. In some cases, you may have to move projects to a different season, while possibly utilizing your same referendum budget, or other funding sources. Funding sources may include ESSER Funds (Elementary and Secondary School Emergency Relief), capital improvement funds, specific state funds, as well as interest earnings or grants.
We regularly break up large school projects by grade and sometimes by classrooms. Site work is considered a separate portion, but it can be further broken out into areas such as playgrounds, parking, and pick-up lanes. When hurdles and difficulties appear, it is easier to adjust if these have already been divided up and analyzed individually.
In addition, establishing the timing of these project components can be instrumental as you consider the purchase of items that require a long lead time. During construction at CPSD, the lead time to attain bar joists and decks was in the 12-16 months’ timeframe. We secured a manufacturing slot during the design process to ensure the materials would be available to meet our construction timeline. This was an arrangement made with manufacturers where we purchased a slot, while allowing time for the team to determine the exact structural specifications.
Always convey challenges to the entire project team to engage more minds in creating solutions.
COMMUNICATION
Communication has always been a vital component of all construction projects. And during demanding times like those we’re currently in, communication plays an even more significant role. Always convey challenges to the entire project team to engage more minds in creating solutions. You want to capitalize upon the education, experience, creativity, and relationships of the entire group.
For example, subcontractors who regularly bid, install, and service equipment can often offer beneficial insights and advice. Mechanical, electrical, and plumbing engineers may be oblivious to a situation in which specified systems and fixtures might currently be difficult to obtain. Subcontractors may be aware of effective alternatives. By communicating with a multi-disciplinary team consisting of construction, engineering, and design professionals, you’ll benefit. You’ll also increase the likelihood of successful completion of your plan.
In a construction project, people too often only see and hear about the challenges and delays. Be sure to accentuate the positive as well. It is wise to look for opportunities to get students, teachers, and the community to participate. With the length of time that it takes to complete a project, they need to experience the progress. Keep them informed. Clintonville made the raising and placing of the final beam a community-wide event. In another school district, we asked students and staff to sign the concrete floor prior to placing the wood gym floor over it. These activities created momentum, collaboration, and enjoyment, and were a cause for celebration.
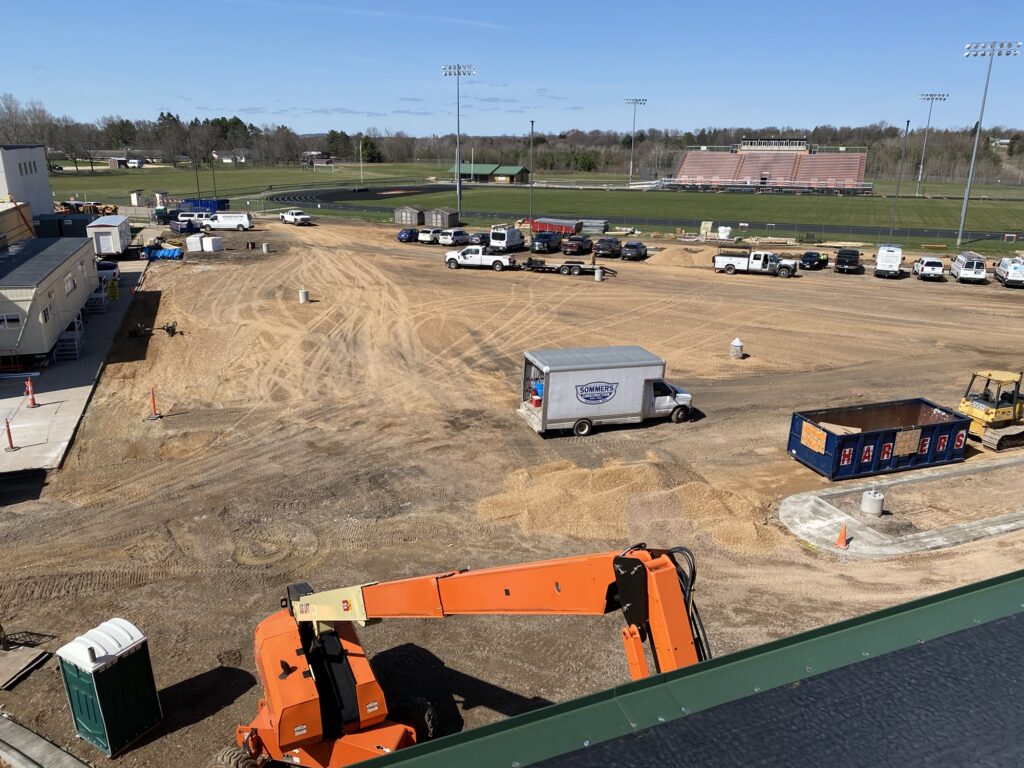
It is important to be aware that, due to supply chain inconsistencies, installation of certain components may not follow the typical order of construction sequencing that provides the greatest efficiency. For instance, the ceiling grid may be installed before the walls are painted. That would not be the desired order, and it may cause a small amount of rework in the future. Another illustration would be that the power supply may not yet be operational, but it may make sense from a scheduling standpoint to proceed with installing the HVAC units. It’s not the order we’d desire, but we need to be agile and always ready to adapt.
FLEXIBILITY
School leadership must also realize that, during the planning and implementation process, selected items will need to change to either accommodate schedule or meet budget. Inflation, workforce challenges, and supply chain issues have significantly impacted the construction industry. To plan for these issues, build in contingencies, allowances, or inflation factors corresponding to the current market and the complexity of your project.
New challenges require new solutions.
Considering these types of challenges, we’re finding ourselves increasingly purchasing materials earlier to ensure we have items when needed. This results in having to identify and obtain larger than normal storage space at the construction site or in a different location. This means we must raise the level of security due to an increase in inventory. Additionally, we need to obtain extended warranties since the materials were not utilized as quickly as usual. New challenges require new solutions.
In Clintonville, we pivoted to accommodate chiller challenges. We had scheduled this project around the cooling season needed for the building. There were continuous schedule delays from the manufacture of the chiller. We ultimately had to be flexible and extend the project to the following season. Be certain not to start a project until the critical materials or equipment are on site.
It is vital for the project team to know where they can be flexible, and what activities must happen precisely as scheduled or planned. Additionally, it needs to be clearly identified and articulated what must be completed to make certain a school can open on time and what items might be considered optional.
OVERCOMING THE OBSTACLES
All the challenges in recent years have forced each of us to think critically. You have developed a myriad of solutions to unprecedented trials. Utilize these skills — and a forward-thinking design and construction partner — to overcome the obstacles facing construction projects, being certain to be flexible, establish priorities, break your project into manageable portions, and communicate actively. Your students, faculty, staff, and community will reap the benefits of great leadership!